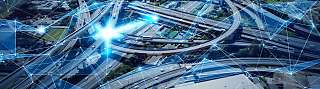

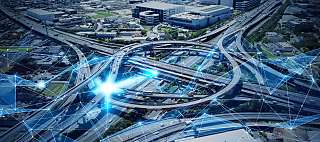
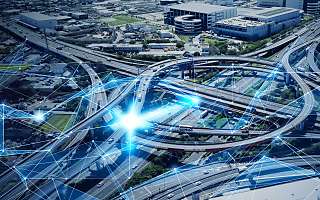
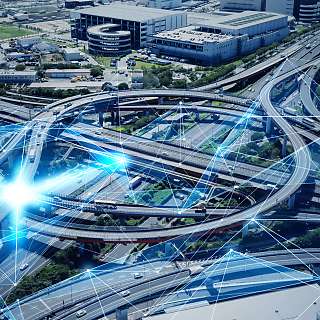
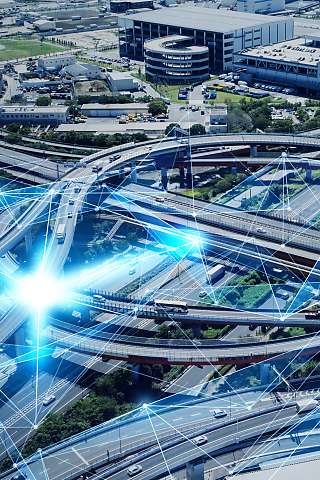
CAN bus is a vehicle bus standard system that enables the communication between multiple vehicle electronic control units. CAN stands for Controller Area Network. Electronic control units (ECUs) are parts of a vehicle that contain information and can sense and share information from other parts of the vehicle.
CAN bus is standard in all vehicles, including cars, trucks, buses, ships, EV batteries, machinery and more.
How do CAN bus systems work?
CAN bus systems act as the nervous system in the human body. ECUs are like the parts of the body and interconnected in a vehicle. Various ECUs may have information that needs to be shared with other parts of the network. It enables each ECU such as engines, antilock braking/ABS, airbags, cruise control, electronic fuel injection, automatic gearbox, and battery systems, to communicate with each other without a central computer.
Essentially, it prepares and broadcasts information, like sensor data, over the CAN bus network. The data is then accepted by all ECUs – then the ECUs decide whether to receive the data or ignore it.
What is a CAN frame?
The communication between the ECUs over the CAN network happens via CAN frames. There are four types of CAN frames:
- Data frame – the only frame for actual data transmission
- Error frame – contains nodes to detect errors
- Overload frame – injects when there is a delay between data and remote frame
- Remote frame – a frame that requests information from a specific identifier
Typical applications for CAN data
CAN bus data frames can be used in several use cases. For example, for fleet managers, logging vehicle data is essential to make informed decisions that reduce fuel costs and improve driver performance. For construction companies that operate with heavy-duty fleet telematics, data from tractors or trucks can be analysed to improve safety and lower costs. For professional service companies that make many deliveries in a day, can help predict and avoid breakdowns by logging CAN data to the cloud. These are just a few cases of logging CAN data.
Webfleet and CAN bus
At Webfleet, we understand the power of using data to optimise performance. That’s why we offer solutions equipped with CAN bus connectivity to help you take your fleet management to the next level.
Interested in how to stay connected to your business with valuable insight that help you boost productivity and improve efficiency? Get in touch with one of our experts today or check out our Webfleet fleet management software.
What are the benefits of CAN bus?
Low costs and straightforward
Because ECUs can communicate on a single CAN system, instead of complex dedicated wiring, it reduces weight, errors and costs.
Centralised
It enables central diagnostics, configuration and data logging on one point of entry through the CAN network.
Robust
Not easily impacted by electric disturbances or electromagnetic interference. The CAN bus standard is ideal for safety-critical applications (e.g. drivers in transport).
Efficiency
Data is prioritised without causing interruption to other frames.
Your consent is required
In this section, external content is being embedded from .
To display the content, your consent is required for the following cookie categories:
- Targeted Advertising
- Analytics & Personalization
- Essential
For further details, please refer to our privacy policy. If you are interested in how ###vendor_name### processes your data, please visit their privacy policy.